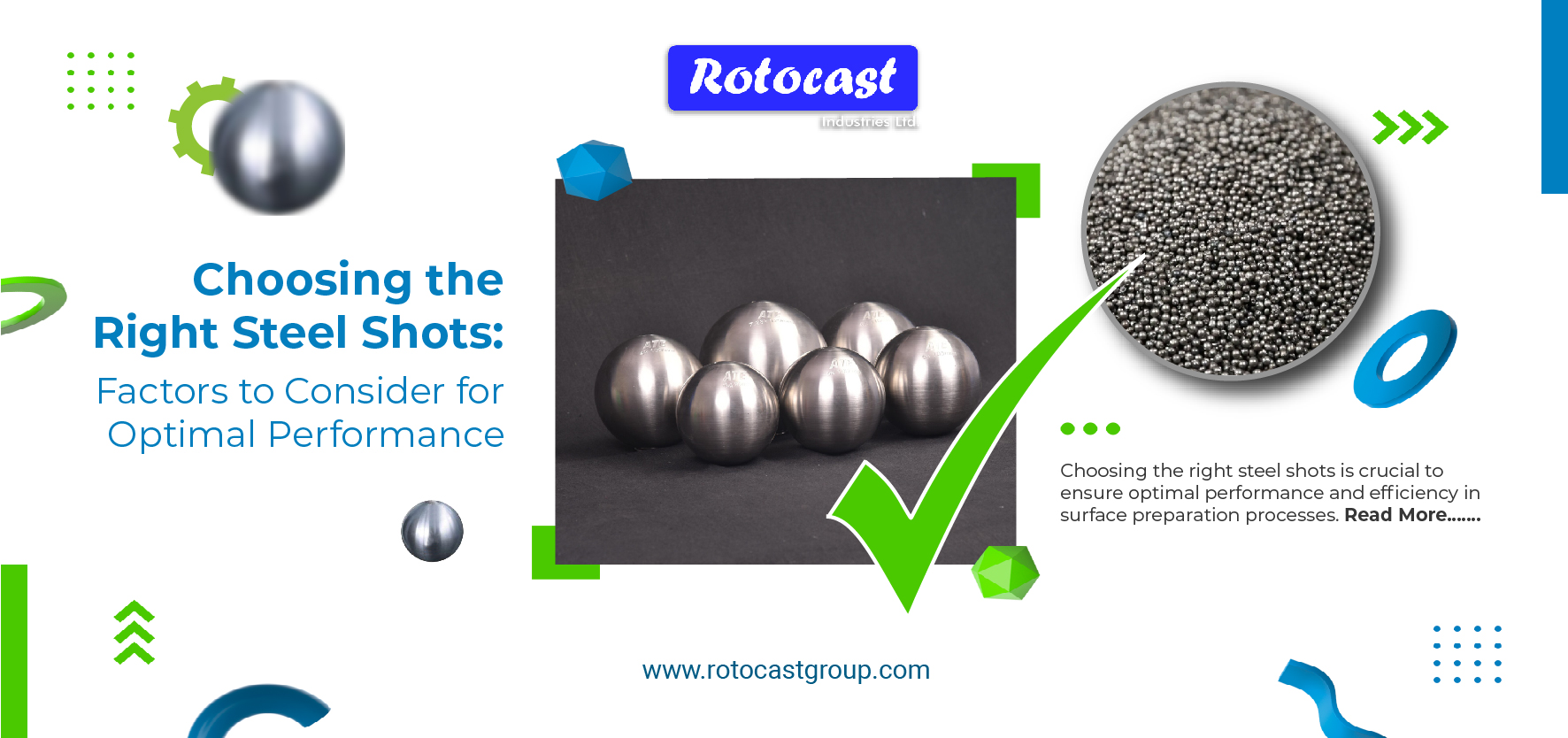
Choosing the right steel shots is crucial to ensure optimal performance and efficiency in surface preparation processes. Various factors come into play when selecting steel shots for specific applications. here, we will discuss the key factors that should be considered to make an informed decision when choosing steel shots.
- Application Requirements: Understanding the specific requirements of the surface preparation application is essential. Consider the type of material being treated, the desired surface finish, and the level of cleanliness needed. Different applications may require different shot sizes, hardness levels, and shapes to achieve the desired results.
- Shot Size: Steel shots are available in various sizes, ranging from small to large. The shot size selection depends on factors such as the type of substrate, the coating or material to be removed, and the desired surface profile. Finer shots are suitable for delicate surfaces or lighter cleaning, while larger shots are more effective for heavy-duty applications.
- Hardness: The hardness of steel shots determines their durability and impact resistance. Harder shots tend to have a longer lifespan and retain their shape better, resulting in improved efficiency and consistent performance. However, excessively hard shots may cause surface deformation or damage. Consider the hardness requirements based on the substrate material and the intensity of surface preparation required.
- Shape: Steel shots are available in different shapes, such as round, angular, or conditioned. The shape affects the aggressiveness of the impact, the surface profile achieved, and the coverage. Angular shots are more aggressive and provide enhanced surface cleaning, while conditioned shots have smoother edges and are often used for peening applications.
- Quality and Consistency: Opt for steel shots from reputable manufacturers known for their quality and consistency. Consistent shot size, shape, and hardness ensure uniformity in the surface preparation process and improve the reliability of results. Quality shots also minimize the risk of defects or contamination that could impact the integrity of the substrate or the coating applied later.
- Equipment Compatibility: Consider the compatibility of the chosen steel shots with the equipment being used for surface preparation. Ensure that the shots are suitable for the blasting equipment, such as shot blasting machines or wheel blast systems, to achieve optimal performance and avoid any equipment damage or inefficiencies.
- Safety and Environmental Impact: Evaluate the safety and environmental aspects associated with the use of steel shots. Consider factors such as dust generation, potential health hazards, and any environmental regulations or restrictions that need to be adhered to. Explore options for environmentally friendly or recyclable steel shots to minimize environmental impact.
In conclusion, selecting the right steel shots for surface preparation involves considering factors such as application requirements, shot size, hardness, shape, quality, equipment compatibility, and safety. Taking these factors into account will help ensure optimal performance, efficiency, and desired surface finish while minimizing risks and environmental impact.
If you are looking for Steel Shots Manufacturer in India. There are a number of reputable steel shots manufacturer in India. One such example is Rotocast Industries Ltd. They excel in providing the best services to client. They have been serving the requirements of steel shot blasting, shot peening and granite cutting for many years.