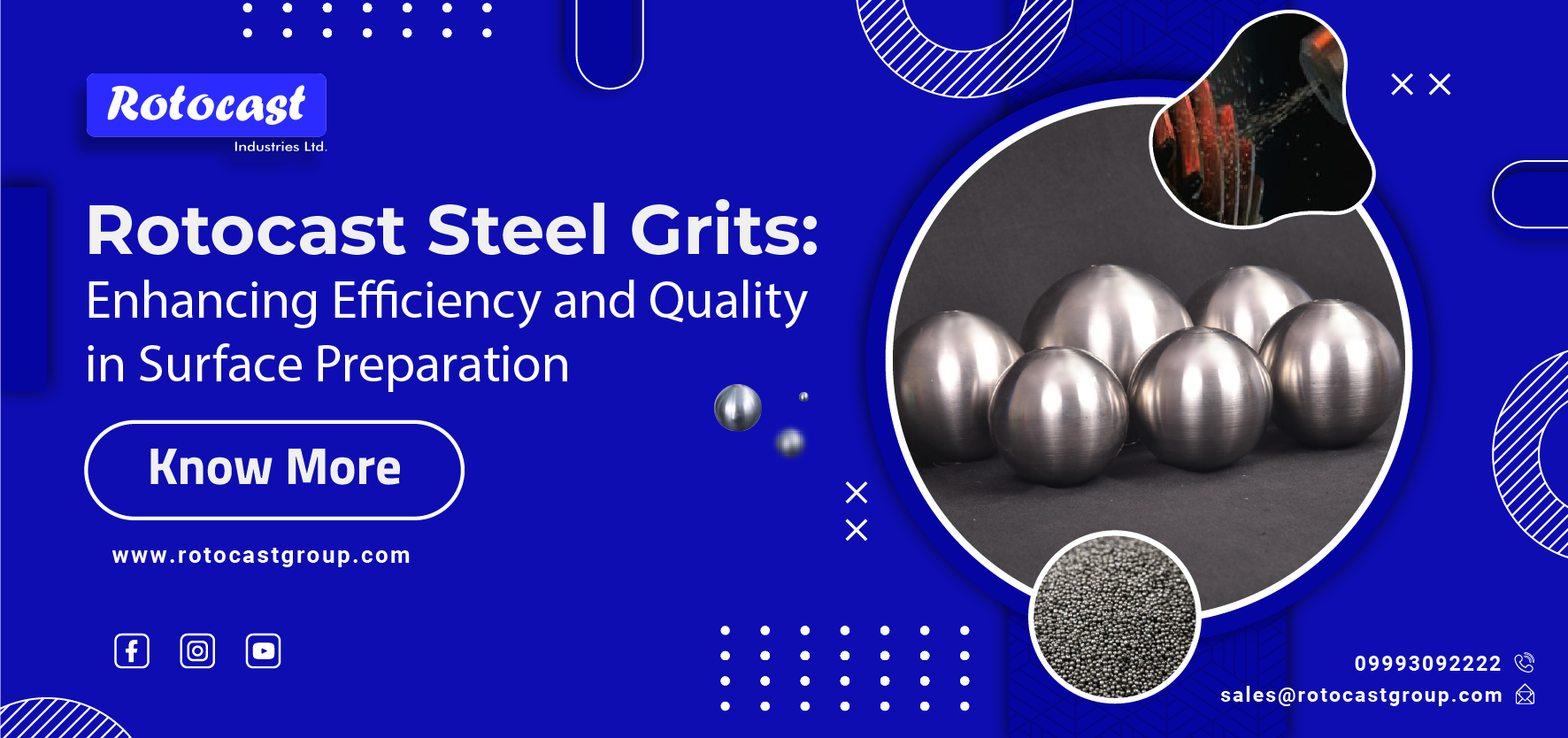
Rotocast Tuff – Steel Grit are made by crushing specially produced Rotocast Tuff – Steel Shot with an extremely specialized process and imported equipment. The totally imported processing line along with the benefits of clean refined steel, special heat treatment cycles, and tight quality controls ensure unmatched performance and life.
A simple inspection under the microscope by your trained lab technician will show that these steel grit are not comparable to any Indian steel grit made till date. In keeping with the modern times and ambitions of our country they are truly – ‘world class’. Here in this article, we will explore the features, advantages, and applications of rotocast steel grits, highlighting how they can enhance efficiency and quality in surface preparation processes.
- Understanding Rotocast Steel Grits: Rotocast steel grits are produced using a specialized manufacturing process known as rotocasting. This process involves centrifugal force, which creates highly spherical steel particles. These particles possess consistent shape and size, resulting in improved performance and uniformity during surface preparation tasks. Discussing the manufacturing process will help readers understand the unique characteristics of rotocast steel grits.
- Advantages of Rotocast Steel Grits: Rotocast steel grits offer several advantages over traditional steel grits. The spherical shape of the particles ensures uniform impact and coverage, resulting in more consistent cleaning, deburring, and descaling. The rounded edges of the particles reduce the risk of surface damage, making them suitable for delicate or precision components. Additionally, the uniform size and shape contribute to longer-lasting performance and reduced dust generation. Highlighting these advantages will demonstrate the value of rotocast steel grits in surface preparation applications.
- Enhanced Cleaning and Surface Conditioning: Rotocast steel grits are highly effective in cleaning surfaces by removing rust, scale, paint, and other coatings. The spherical shape allows them to reach into crevices and hard-to-reach areas, ensuring thorough cleaning. Moreover, the uniform size and shape contribute to consistent surface conditioning, preparing the substrate for subsequent processes such as painting or coating. Discussing these cleaning and surface conditioning benefits will help readers understand how rotocast steel grits can improve their surface preparation outcomes.
- Reduced Surface Roughness and Improved Consistency: Rotocast steel grits are known for their ability to achieve desired surface roughness while maintaining consistency. The spherical shape and controlled size distribution of the particles enable precise control over the surface profile, ensuring adherence to specifications and coating requirements. This feature is particularly beneficial in applications where a specific surface roughness is essential for coating adhesion or aesthetic purposes. Emphasizing the reduced surface roughness and improved consistency will demonstrate the advantages of using rotocast steel grits in surface preparation.
- Applications and Industry Uses: Rotocast steel grits find applications in various industries, including automotive, aerospace, foundries, and metal fabrication. They are particularly suitable for cleaning and surface preparation of precision components, molds, and delicate parts. Discussing specific industry uses and applications will provide readers with a better understanding of where rotocast steel grits can be effectively employed.
Conclusion: Rotocast steel grits offer unique advantages in surface preparation, including enhanced cleaning, surface conditioning, reduced surface roughness, and improved consistency. Their spherical shape, uniformity, and controlled size distribution contribute to superior results and increased efficiency. By utilizing rotocast steel grits in surface preparation processes, industries can achieve higher-quality finishes, reduce surface damage, and optimize overall productivity. Understanding the benefits and applications of rotocast steel grits will empower professionals to make informed decisions and improve their surface preparation outcomes.