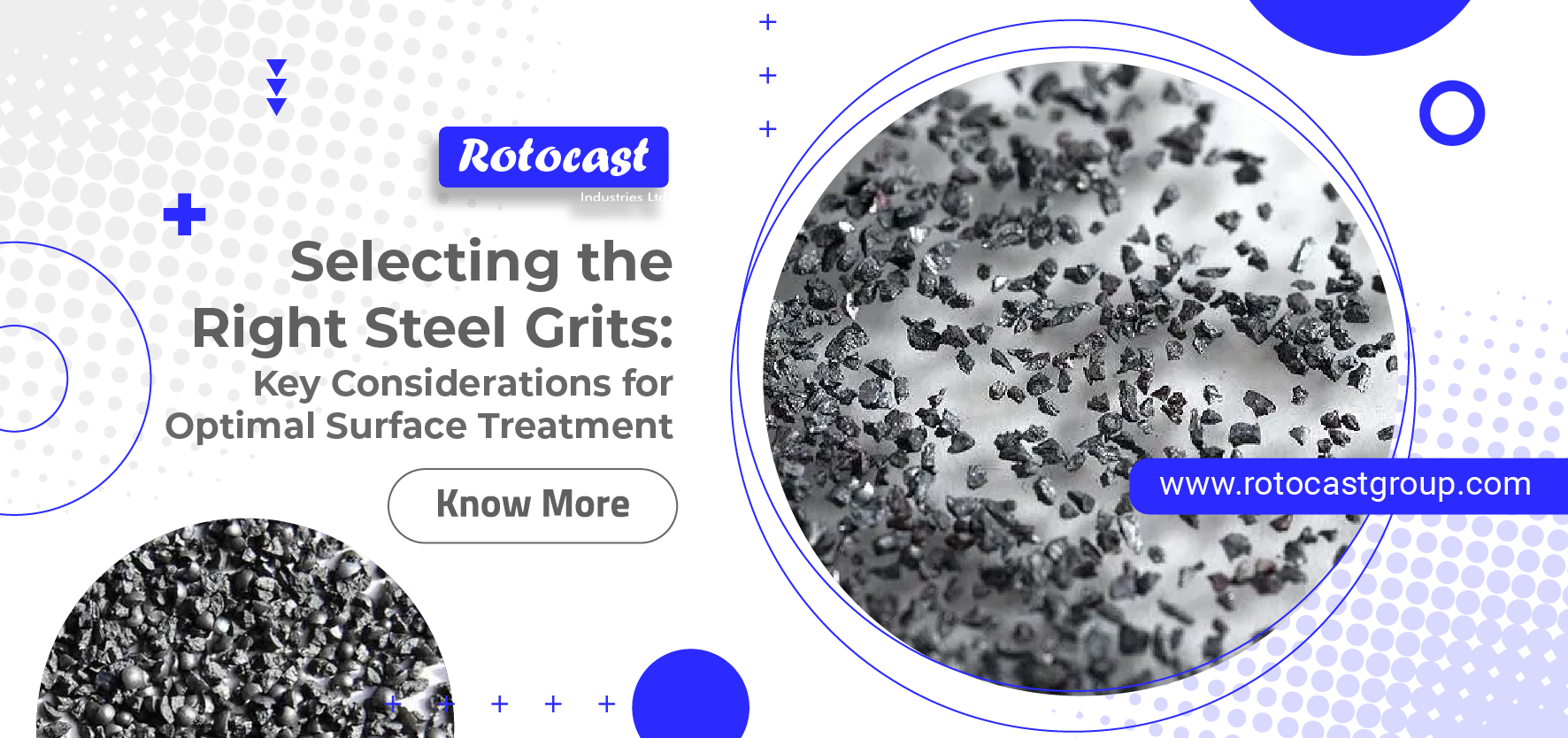
Surface treatment is a critical process in various industries, including manufacturing, construction, and metal fabrication. Steel grits are commonly used as an abrasive media for surface treatment due to their exceptional cutting ability and durability. However, choosing the right steel grits for your specific application is crucial to achieving optimal surface treatment results. Here, we will discuss key considerations to help you select the right steel grits for your surface treatment needs.
- Particle Size
Particle size or granulation is a vital factor when selecting steel grits for surface treatment. Steel grits are available in a range of sizes, typically indicated by a designated mesh size or grit size number. The particle size directly affects the surface profile and the level of aggressiveness during the treatment process. Finer grit sizes, such as G80 or G120, produce a smoother surface finish and are suitable for applications that require minimal material removal or a fine surface profile. Coarser grit sizes, such as G25 or G40, provide more aggressive cutting action and are ideal for heavy-duty applications or when significant material removal is required. Consider the desired surface profile and the thickness of coatings or contaminants to choose the appropriate particle size for your specific application.
2. Hardness
The hardness of steel grits is a crucial factor in their performance during surface treatment. Steel grits are manufactured in different hardness levels, typically categorized as GP (general purpose) or GL (harder) grits. GP grits are softer and more malleable, making them suitable for applications that require controlled surface roughness or minimal substrate damage. GL grits, on the other hand, are harder and more resilient, providing more aggressive cutting action and faster material removal. Consider the nature of the surface being treated, the desired level of aggressiveness, and the tolerance for substrate damage to select the appropriate hardness level of steel grits.
3. Shape
Steel grits are available in different shapes, including angular and round. The shape of the grit particles influences their cutting ability and surface impact. Angular grits have sharp edges and corners, delivering a more aggressive cutting action and higher surface roughness. They are suitable for applications that require significant material removal or surface profiling. Round grits, on the other hand, have smoother edges, resulting in a less aggressive cutting action and a smoother surface finish. Round grits are ideal for applications that require controlled roughness or when minimizing substrate damage is crucial. Consider the desired surface roughness, the coating thickness, and the sensitivity of the substrate when choosing between angular and round steel grits.
4. Recyclability
Recyclability is an important consideration in terms of cost-effectiveness and environmental impact. Steel grits can be recycled and reused multiple times before they become too worn to provide effective surface treatment. The recyclability of steel grits reduces the overall abrasive consumption, resulting in cost savings and a reduction in waste generation. However, it’s important to note that the recyclability may vary depending on the type and quality of the grits. Some specialized or low-cost steel grits may have limited recyclability due to their lower durability. Evaluate the recyclability of the steel grits and consider the cost-effectiveness and environmental implications based on your specific requirements.
5. Application Requirements
Consider the specific requirements of your surface treatment application. Different applications, such as paint removal, surface profiling, or deburring, may have unique demands in terms of surface finish, coating removal efficiency, or substrate integrity. Evaluate the application requirements, including the material being treated, the desired surface profile, the coating thickness, and any industry standards or specifications that need to be met.
Rotocast is one of the most oldest and reliable manufacturers in the field of quality Steel Abrasives [Steel Shot and Steel Grit] and Alloy Steel Castings. We have been serving the requirements of steel shot blasting, shot peening and granite cutting for many years now. Having served the industries for nearly 30+ years our client list includes the who’s who of reputed Auto components, Cement, Steel, Mining, Engineering, Foundry & Forging Industries in India and abroad.