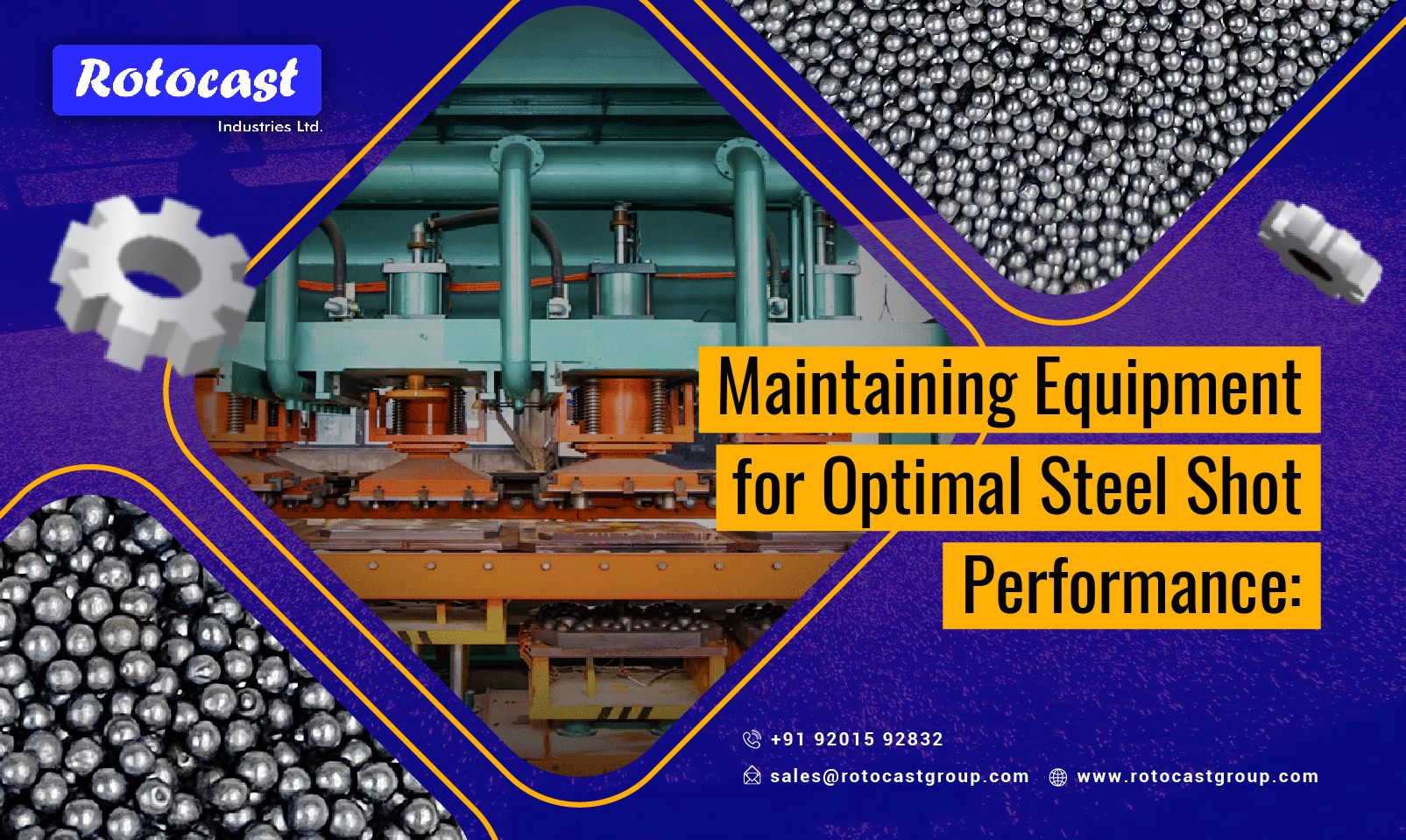
In industries where steel shot is a crucial component, such as manufacturing, construction, and automotive sectors, ensuring optimal performance is paramount. However, achieving consistent results requires more than just high-quality steel shots; it demands diligent maintenance of the equipment used in the process. From blast machines to conveyors, each component plays a vital role in the efficiency and effectiveness of steel shot operations. Here, we delve into the importance of maintaining equipment for optimal steel shot performance and explore key practices to uphold.
Preserving Blast Machines: Blast machines are central to steel shot operations, serving as the primary apparatus for propelling abrasive materials onto surfaces. Regular inspection and maintenance of blast machines are essential to prevent breakdowns and maintain performance. This includes checking for worn or damaged parts, such as nozzles, hoses, and valves, and promptly replacing them as needed. Additionally, ensuring proper abrasive flow and pressure settings is crucial for consistent and efficient blasting.
- Cleaning and Calibrating Shot Peening Equipment: Shot peening equipment, commonly used in industries like aerospace and automotive manufacturing, requires meticulous cleaning and calibration to ensure precise shot delivery. Any contaminants or irregularities in the shot stream can compromise the integrity of the peening process, leading to subpar results. Regular cleaning of nozzles, sieves, and hoppers, along with calibration checks, helps maintain optimal shot size distribution and coverage, thereby enhancing the effectiveness of shot peening operations.
- Inspecting Conveyor Systems: Conveyor systems play a vital role in transporting steel shot within facilities, and their proper functioning is crucial for seamless operations. Regular inspection of conveyor belts, rollers, and pulleys is essential to identify signs of wear or damage that could impede the movement of shot. Additionally, ensuring proper alignment and tensioning of conveyor components helps prevent jams and ensures the smooth flow of steel shot throughout the production process.
- Lubricating Moving Parts: Many equipment components involved in steel shot operations contain moving parts that require lubrication to reduce friction and prevent premature wear. This includes bearings, gears, and drive mechanisms. Implementing a routine lubrication schedule using appropriate lubricants helps prolong the lifespan of equipment and maintain optimal performance. However, it’s essential to follow manufacturer recommendations regarding lubrication intervals and types of lubricants to avoid over-lubrication or using incompatible products.
- Implementing Preventive Maintenance Programs: To ensure consistent performance and minimize downtime, implementing preventive maintenance programs is invaluable. These programs involve scheduling regular inspections, cleaning, and servicing of equipment based on predetermined intervals or usage thresholds. By identifying and addressing potential issues proactively, preventive maintenance helps prevent costly breakdowns and extends the service life of equipment.
In conclusion, maintaining equipment for optimal steel shot performance is critical for achieving consistent results and maximizing operational efficiency. From blast machines to conveyor systems, each component requires regular inspection, cleaning, and maintenance to ensure smooth operations. By prioritizing preventive maintenance practices and adhering to manufacturer recommendations, industries can enhance the longevity and effectiveness of their steel shot equipment, ultimately leading to improved productivity and quality of end products.