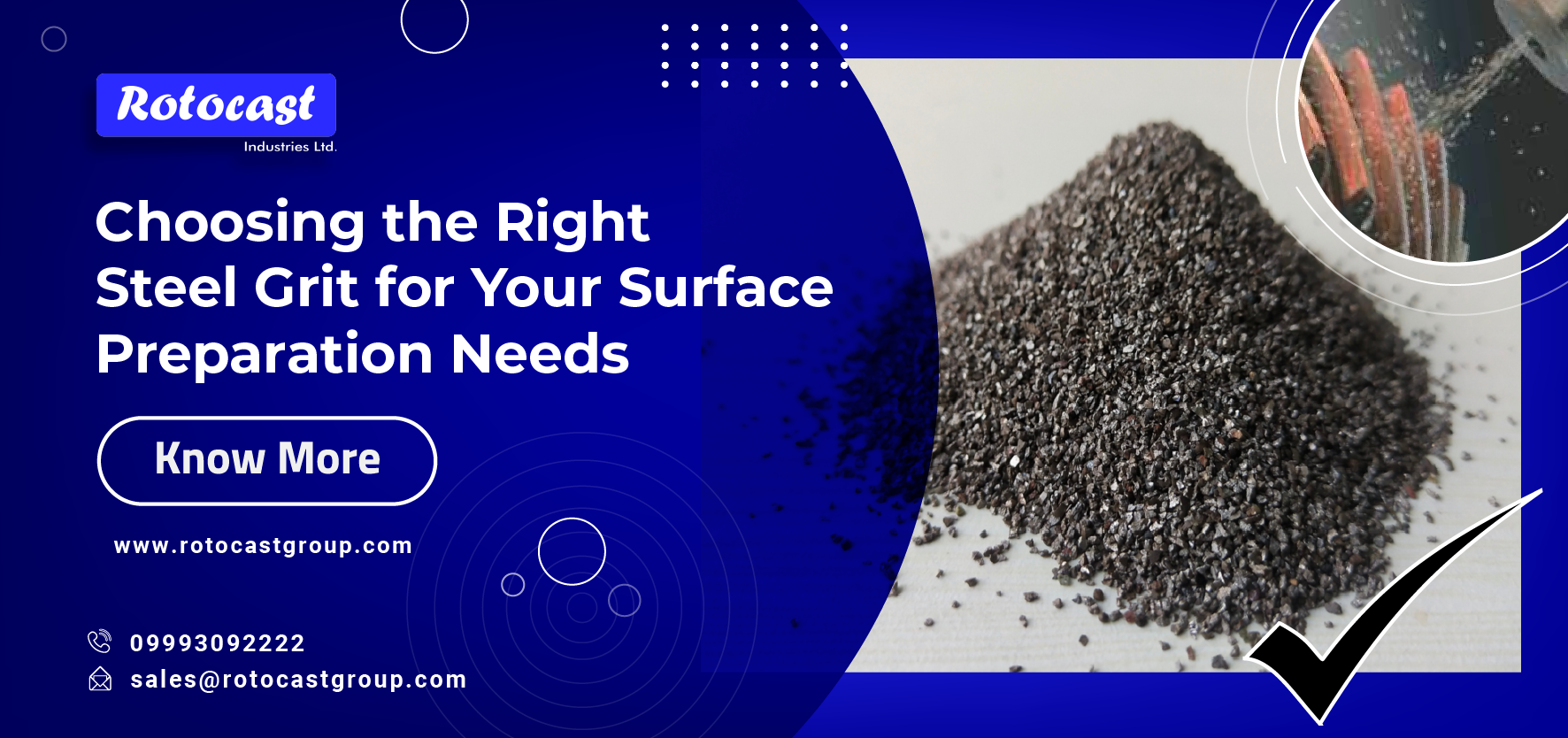
Steel grit is available in different sizes and grades, each designed to cater to specific surface preparation requirements. Selecting the appropriate steel grit for your project is crucial to achieve optimal results. Here we will discuss the factors to consider when choosing the right steel grit for your surface preparation needs, helping you make an informed decision and achieve the desired outcome.
- Understanding Steel Grit Sizes and Grades: Steel grit is available in various sizes, commonly referred to as grit sizes or mesh sizes. These sizes determine the particle diameter and impact energy, affecting the efficiency and aggressiveness of the blasting process. Explaining the concept of grit sizes and their relation to surface profile and coating adhesion will provide readers with a fundamental understanding of how to select the right size for their specific application.
- Surface Material and Condition: Different surface materials and conditions require different steel grit properties. For instance, softer metals may require a less aggressive steel grit to avoid surface damage, while heavily corroded surfaces might require a more abrasive grit for effective cleaning. Discussing the importance of considering the surface material and its condition will help readers identify the appropriate steel grit for their specific project.
- Desired Surface Profile and Coating Requirements: The desired surface profile and coating requirements also play a significant role in steel grit selection. Some applications may require a specific surface roughness or anchor pattern to ensure proper adhesion of coatings or paints. Providing guidance on matching the steel grit size and hardness to the desired surface profile will assist readers in achieving the intended coating performance.
- Equipment and Blasting Parameters: The type of blasting equipment and its capabilities should also be considered when selecting steel grit. Different equipment may have specific requirements or limitations regarding the type and size of abrasive material used. Additionally, the blasting parameters, such as nozzle pressure and distance, should be optimized to achieve the desired results. Including tips on matching steel grit properties with the equipment and adjusting blasting parameters can help readers maximize the effectiveness of their surface preparation process.
- Industry Standards and Manufacturer Recommendations: Highlighting industry standards and manufacturer recommendations for steel grit selection can provide valuable insights. Industry standards, such as ISO 11124 and SAE J444, provide guidelines for grit sizes and properties. Manufacturers often provide technical specifications and recommendations based on their products’ performance. Encouraging readers to consult these standards and manufacturer guidelines will assist them in making informed decisions.
Conclusion: Choosing the right steel grit for surface preparation is crucial to achieve the desired surface profile, coating adhesion, and overall project success. By considering factors such as grit sizes, surface material and condition, desired surface profile, equipment compatibility, and industry standards, you can make an informed decision and select the most suitable steel grit for your specific needs. Understanding these considerations will help optimize your surface preparation process and ensure superior results.
Rotocast steel grits offer unique advantages in surface preparation, including enhanced cleaning, surface conditioning, reduced surface roughness, and improved consistency. Their spherical shape, uniformity, and controlled size distribution contribute to superior results and increased efficiency. By utilizing rotocast steel grits in surface preparation processes, industries can achieve higher-quality finishes, reduce surface damage, and optimize overall productivity.