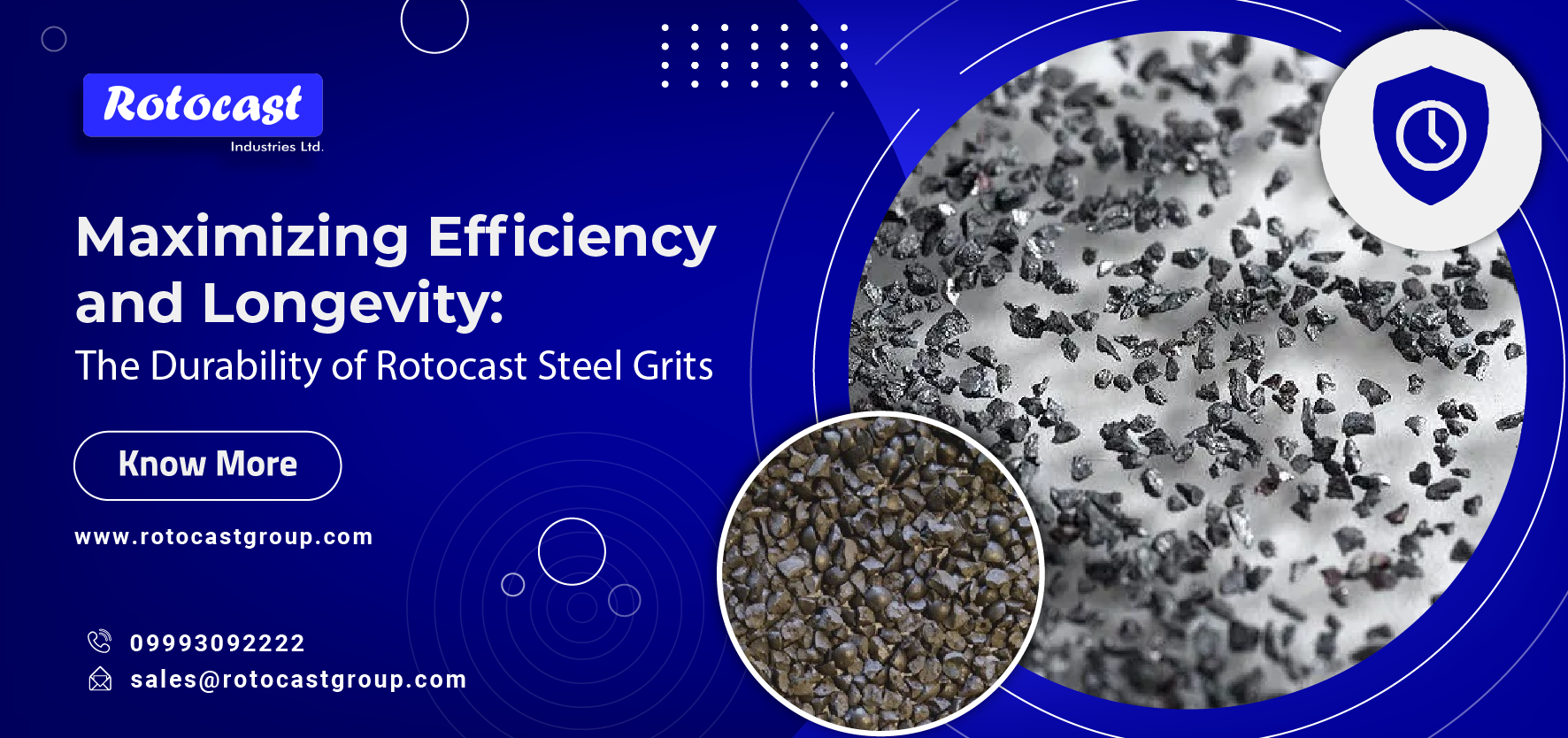
When it comes to surface preparation, durability is a crucial factor to consider in the selection of abrasive materials. Rotocast steel grits are known for their exceptional durability, making them a preferred choice in various industries. Here, we will delve into the durability aspects of rotocast steel grits and explore how they can maximize efficiency and longevity in surface preparation processes.
- The Manufacturing Process of Rotocast Steel Grits: To understand the durability of rotocast steel grits, it’s important to delve into their manufacturing process. Explain the rotocasting process, where molten steel is atomized and solidified into spherical particles. This unique manufacturing technique ensures the formation of durable, high-quality steel grits that can withstand the rigors of surface preparation applications.
- Superior Resistance to Wear and Fracturing: Rotocast steel grits are designed to exhibit exceptional resistance to wear and fracturing. Their spherical shape and consistent hardness allow for more efficient and consistent cutting action over extended periods. This resistance to wear and fracturing minimizes the need for frequent replacement during surface preparation, resulting in cost savings and increased productivity.
- Extended Reusability and Reduced Consumption: The durability of rotocast steel grits contributes to their extended reusability. Due to their ability to withstand multiple cycles of surface preparation, they can be recycled and reused several times before needing replacement. This extended reusability reduces consumption and waste generation, making rotocast steel grits a sustainable and cost-effective choice.
- Reduced Dust Generation: In surface preparation processes, dust generation can be a concern both for operational efficiency and worker safety. Rotocast steel grits are known for their low dust generation, which is beneficial for maintaining a clean working environment, minimizing cleanup efforts, and reducing the risk of respiratory issues for workers. The durability of rotocast steel grits ensures that the particles maintain their integrity, resulting in less fine particulate matter being generated during blasting operations.
- Compatibility with High-Pressure Blasting Systems: Rotocast steel grits are well-suited for high-pressure blasting systems due to their durability. They can withstand the higher impact energies associated with these systems without excessive fracturing or breakdown. Discussing their compatibility with high-pressure blasting systems will highlight the suitability of rotocast steel grits for demanding surface preparation applications.
- Applications and Industries: Highlight the industries and applications where the durability of rotocast steel grits is particularly valuable. These may include shipbuilding, oil and gas, metal fabrication, and automotive sectors, among others. Discuss how the durability of rotocast steel grits contributes to the efficient and effective cleaning, deburring, and descaling of various surfaces in these industries.
Conclusion: The durability of rotocast steel grits sets them apart as a reliable and long-lasting abrasive material for surface preparation. With superior resistance to wear and fracturing, extended reusability, reduced dust generation, and compatibility with high-pressure blasting systems, rotocast steel grits maximize efficiency and longevity in surface preparation processes. By choosing these durable abrasives, industries can achieve consistent and high-quality results while optimizing cost savings and minimizing environmental impact.